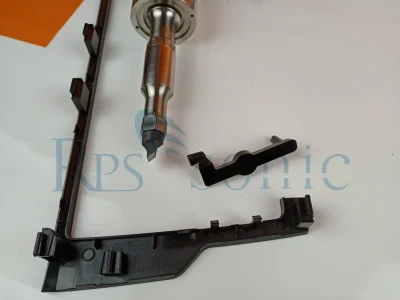
20kHz Ultrasonic Cutting for Industrial Applications on Hard and Soft Materials
Basic Info
Model NO. | RPS-C20 |
Classification | Ultrasonic Cutting Device |
Applicable Process | Process Materials |
Suitable Substrates | Plastic, Fabric, Non Woven |
Packaging Material | Carton |
Blade Thickness | 0.2mm ,Customized |
Blade Material | Rapid Steel |
Operation Machine | Robot Arm |
Power Supply | Ultrasonic Digital Generator |
Power | 1000W |
Power Output | Infinitive Adjustment |
Transport Package | Carton |
Specification | 20Khz |
Trademark | RPS-Sonic |
Origin | China |
HS Code | 8515900090 |
Production Capacity | 200/Month |
Product Description
20khz Ultrasonic Cutting for Industrial Applications on Hard And Soft Materials
Frequency | 20Khz |
Frequency adjustment | Auto-tracking type |
Max. power output | 1000W |
Power output | Infinitive adjustment |
Power supply | AC200V 50/60Hz |
Outer dimension (mm) | 120*120*380 |
Weight | 6kg |
Blade thickness | 1mm |
What's the principle of ultrasonic cutting?
RPS-SONIC offers high quality ultrasonic food cutting components, including ultrasonic generators, transducers, guillotines and slitters.
Ultrasonic food processing involves a vibrating knife (guillotine) producing a nearly frictionless surface that minimizes buildup on the blade surface. The ultrasonic blades cleanly cuts sticky products and inclusions such as nuts, raisins & morsels without displacement. Ultrasonic cutting is used by many of the world's largest and most prestigious food producers.
RPS-SONIC has worked in ultrasonic area more than 10years. RPS-SONIC'S ultrasonic components are a widely used and proven technology. The "guillotine" blades are crafted in titanium and employ the latest FEA design technology for trouble free operation and reliability.
Ultrasonic cutting, guillotining or sititing, can be thought of as an enhancedconventional cutting process. The blade has a cutting edge and a shank. Theultrasonic vibration of 20kHz moves the cutting tip rapidly forward andback, superimposed on a forward movement of perhaps 5 m/min. Thisoscillating movement applies an intermittent cutting force to the crack tipand so controls this crack (cut) propagation or growth minimizing the stresson the bulk material. The repeated application of the cutting tip to theproduct applies a local fatiguing effect which reduces significantly theoverall required force to break the bonds of the bulk material. A usefulanalogy is the hammer drill or the pneumatic road drill concepts. A secondaspect to ultrasonic cutting is the friction reduction of the blade shank as itfollows the tip into the opening cut. In conventional cutting the blade has tocompress the bulk material to allow a gap the width of the blade to passthrough; the compression to the bulk applies a tensile rupturing force at thecrack tip. With ultrasonic cutting the whole blade moves or vibratescontinuously as it stretches and contracts. This very high-frequency movement effectively reduces the co-efficiency of friction to a verylow level, enabling the blade to slide through the bulk material withconsiderable reduction to the compression and contact, giving a forcereduction and decreased smearing effects.The use of ultrasonics is becoming increasingly important for the foodindustry.Ultrasound in Food Processing enables scientists, engineers andmanagers in food manufacturing to make informed choices about anew and important area of research and development. It will also be avaluable reference to people working in other areas of ultrasoundresearch and instrument manufacture.wide ultrasonic food cutting machine Vibrating Guillotine Knives
Adantages
Cleaner cuts for outstanding aesthetics on layered products
Reduced downtime for cleaning and reduce waste
Flexibility & increased productivity
Larger processing windows
Characteristics of ultrasound blades:
- Ultrasonic blades may vary in length and height, depending on clients' specific requirements
- Knife shapes and dimensions are studied by our technical department after taking into account details such as food thickness, ingredients,dimensions, density and additional special features
- They are made out of titanium and comply with all health and organoleptic standards regarding the automation field.
Target Materials
*Resin plate
*Glass fiber (GFRP)
*Formed decorative film
*Foam
*Blow-molded parts
*Injection-molded parts
*Carbon fiber (CFRP)
*Aluminum foil composites
*Non-woven fabrics
*Controlled-depth kiss cutting
BENEFITS OF ROBOTIC ULTRASONIC CUTTING
- Process flexibility
- Enhanced precision
- Cleaning edages
- cost reduce
- Energy efficient
- worker safety
- Enviroment Friendly
- No water waste disposal